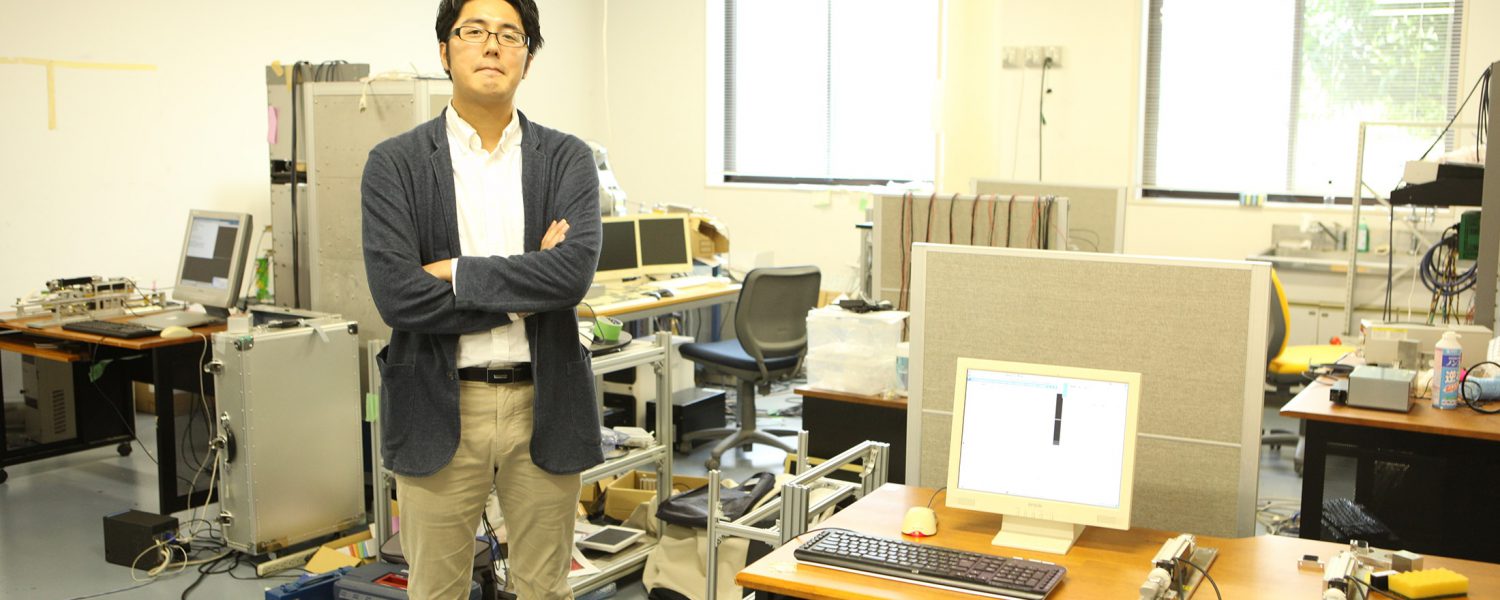
日本発、機械に「触覚」を与える革新的技術
職人から医師まで、機械には代替不可能な手仕事の世界。
その実現のカギを握る「触覚」を実装する夢の技術が今、日本から世界へ羽ばたこうとしているーー。
慶應義塾大学の「リアルハプティクス」技術で社会貢献を目指す新進ベンチャー、モーションリブ。
その驚くべき実力と大いなる可能性が、ここに。
触覚を機械に与える「リアルハプティクス」技術とは
私たちのミッションは、慶應義塾大学が開発した「リアルハプティクス」技術の実用化を通して社会に貢献することです。まず「リアルハプティクス」とは何かについてご説明しましょう。近年、ヴァーチャルリアリティ(VR/仮想現実)技術の発展に伴い、映像の中の世界で触れたものの手触りが装置で再現されるなど、触覚を通して情報を伝達する「ハプティクス」技術が話題になりつつあります。これは主に機械が人間に対して感触を提示する技術といえます。
それに対して、私たちが提唱する「リアルハプティクス」はいわば、人間が皮膚感覚として知覚できる力触覚(りきしょっかく)を機械に与える技術です。人に触覚を伝達するだけではなく、その感覚を機械にも与えることで、機械自身がより繊細な作業をすることができるようになるというわけです。
その上で、機械が触覚を感知するためには、従来の技術では様々なセンサーが必要でした。しかし、私たちのリアルハプティクス技術は力センサーがなくても触覚を感知し、さらにそれを人間に伝達することができます。慶應義塾大学ハプティクス研究センターと共同開発した技術によって、位置の情報からそこに発生する力の大きさを推定し、感触を再現する計算を行う仕組みです。
その機能を担うのが、私たちが開発した力触覚コントローラー「ABC-CORE」。この小さなチップをロボットなどのモーター部分に取り付けるだけで、力センサーを用いた場合と同じ精度で力を計測することが可能です。力センサーの多くは繊細で扱いが難しく、また過大な力が加わるような現場では故障する可能性もあり、導入が難しいケースが多いと聞きます。しかし、力センサーを使わない方式の「ABC-CORE」にはそのようなリスクがなく、様々な場面で活用の機会を見込めるはずだと考えています。
ロボットに“柔らかい”力加減をもたらす技術の衝撃
この技術の実用化に取り組んだきっかけは2002年、当時学生だった弊社CTOの飯田が世界で初めて感触を伝達する実験に成功したこと。私自身も09年から14年にかけて慶應義塾大学理工学部の大西公平教授の研究室で、技術の精度を高める研究や性能の検証などに携わりました。博士課程の修了後は就職をする予定でしたが、リアルハプティクス技術の可能性に心惹かれて、事業化に参加することになったのです。
事業化への流れとしては、まず2014年末に慶應義塾大学ハプティクス研究センターが開設され、企業との共同研究に着手しました。その手応えを得て「ABC-CORE」の量産体制を確立するべく、モーションリブ株式会社を2016年春に設立。現在は、共同研究の企業各社に「ABC-CORE」を貸与して応用製品の試作開発を進めていただき、様々な分野で製品化を目指しているところです。
リアルハプティクス技術の特徴は、大きく4つの機能で説明できます。感触を伝達する機能、感触を記録する機能、感触を編集する機能、そして、記録したデータを使って同じ動作を再現する機能です。これらの機能を組み合わせることで、熟練職人や医師などの手の動作を記録し、それをロボットが再現することができるようになります。つまり、これまでは自動化が難しく人手が必要だった作業に、ロボットを導入することが可能になるのです。
例えばガラスをはめ込むような作業は、状況に応じた繊細な力加減が要求されるために、ロボット化が難しいとされてきました。力をやさしく加減することは人間にとってはごく自然な行為ですが、従来の産業用ロボットは一定の出力で動くだけ。こうした機械のあり方を私たちは“固い”技術と呼んでいます。そこに力触覚の技術を応用して、ロボット自身が触覚に応じて適切に“柔らかく”動くようになれば、機械と人間との関係に大きな変化をもたらすでしょう。
それくらい、この技術には大きなインパクトがあります。そして、世界的に見ても慶應義塾大学の論文数と学会発表数は群を抜いています。デモンストレーションを目にした海外の研究者や技術者からは驚きのあまり、「何か別の仕掛けがあるだろう」と疑われるほどです。
しかし、その技術を世の中へ広めていくためには、経営だけでなくいろいろなノウハウが必要になります。とくに私たちのケースは技術応用の先行事例がほとんどないため、KIIのサポートはとても心強い限りです。資金調達をはじめ、技術のリサーチから人材の確保、情報発信の部分まで、幅広い面で助けていただいているところです。
いよいよ実用化。人間と機械の革新的な未来ビジョン
現在の課題は、この技術をより身近で使いやすく、そしてわかりやすく世の中へ伝えていくこと。製造業だけでなく自動車や医療など、非常に多岐にわたる領域に適用できる技術のため、より多くの企業に手を挙げていただき、共同開発を進めていきたいと考えています。
例えば掃除機に導入すれば、吸い込む感触を通して床の素材の違いを感知し、より最適な力加減を自動的に判断してくれるようになるでしょう。自動車であれば、砂利道や凍った路面などの感触をハンドルに伝えることで、より感覚的で安全な運転が可能になります。自動車のパワーウィンドウや自動ドアに導入すれば、“柔らかい”動作によって指挟みなどの事故を防ぐことができます。介護や医療の現場に導入すれば、優れた技能を持つ人の体の動きをデータとして取得することで適切な力加減を再現しつつ、そのデータを元に治療の効果を分析・活用していくことも可能です。
触感は人間の五感の中でも最初に備わった機能ですが、言葉や視覚情報で共有することが難しいため、これまでは暗黙知の領域とされてきました。日本のものづくりの世界では熟練職人の技術をいかに継承していくかが問われていますが、その動きとともに力加減を記録できたなら、暗黙知を含んだ手技を後世に残すことができるようになるでしょう。
さらに、この技術をAI(人工知能)と組み合わせることによって、これまでにない展望が開けるかもしれません。AIは人間の脳に喩えられますが、リアルハプティクス技術は脳がやりたいと思う動きを機械の体に与える技術といえます。その感触がAIにもたらされることで、これまでにない進化が見込まれます。
リアルハプティクスによって、労働現場のロボット化など産業のあり方はもちろんのこと、より安全・安心な暮らしを実現することができる。すべての人の幸せで豊かな未来のために、この技術を世界中に届けていきたいと思います。
【公式サイトへのリンク】
https://www.motionlib.com/